前副车架上部主体件回弹消除方法研究
文/赵锋·中国第一汽车股份有限公司
乘用车的安全性取决车架总成安全性,而整个车架总成中零件材料多为高强板,高强板零件尺寸的合格稳定直接决定车架振动试验的合格数据,下面将详细的说明通过零件扫描分析、提取回弹数据,并对拉延模具及整形模具型面进行回弹补偿修改,消除前副车架上部主体件回弹缺陷的方法。
复杂成形的高强板前副车架上部主体件,造型角度差异性比较大,形状复杂,一次成形难度大。尤其造型深度段差较大时出现的内部褶皱问题,四角回弹扭曲问题,处理起来更是困难。本文主要阐述TRIP600 高强板前副车架上部主体件一次成形过程中,左右两侧中部表面褶皱引起的回弹和四角回弹扭曲的优化方法。从产品造型、拉延模具及整形模具回弹补偿、优化工艺控制等几个方面,依托扫描分析,合理运用回弹系数,快速直接的解决了前副车架上部主体件回弹扭曲问题。
前副车架上部主体件回弹扭曲问题分析
问题描述
某车型前副车架上部主体件选用材料为DP590R,料厚1.2mm,出件后回弹严重,四角回弹区域在检具上的S 面间隙超差,中部翻边面不平正回弹,总成激光焊接间隙超差,如图1 所示,直接影响整个车架总成的焊接尺寸,属于整车安全不可接受缺陷。
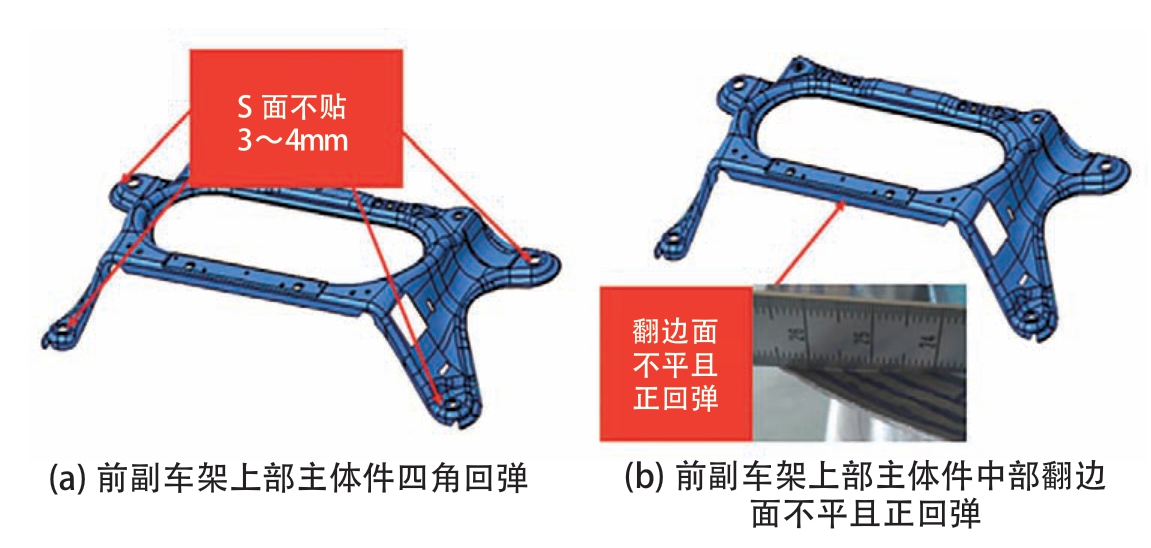
图1 前副车架上部主体件回弹示意图
前副车架上部主体件回弹成因分析
我们在成因分析时,首先确认工艺设计合理性,再通过扫描分析,确认起皱对回弹的影响,确认最终产品变化趋势,结合试制出件状态,考虑实际出件状态,分析变化趋势,确定影响因素。
⑴工艺分析。工艺排布设计中,为了更好的保证制件的形状与尺寸满足设计要求,拉延模具设计成浅拉延结构,修边为一次性外部修边完成,翻边整形同时进行,各个角度冲孔分为两序完成,左右两侧对称,前后两侧不对称。
⑵实际出件扫描分析。实际出件扫描分析中,从正面状态可以看出左右两侧正成形存在负向的回弹,反成形存在正向的回弹,且左右侧不对称;前后侧正成形回弹方向不一致,且前后不均匀,如图2 所示,不对称的回弹会有扭曲趋势,四角回弹状态将不一致。
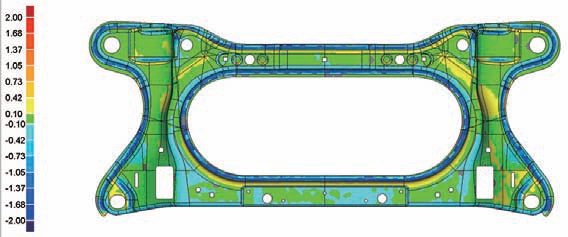
图2 扫描分析中主体件正面状态示意图
实际出件扫描分析中,从侧面状态可以看出中部反成形存在正向的回弹,且不对称,前后侧正成形回弹方向不一致,且前后不均匀,如图3 所示,不对称的回弹会有扭曲趋势,四角回弹状态将不一致。
⑶试制件成形分析中,为了能够利用简易工装压出可以焊接试制的制件,以成形模具为胎模进行压制,选用材料为DP590R,并采取封闭成形,来控制试制零件回弹。如图4 所示,简易工装在慢速油压机上阶段性成形制件,定型比较稳定,但是左右两侧中部位置存在褶皱。
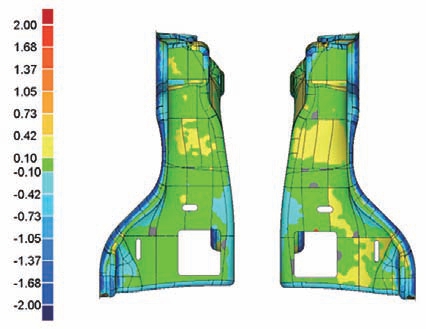
图3 扫描分析中主体件侧面状态示意图
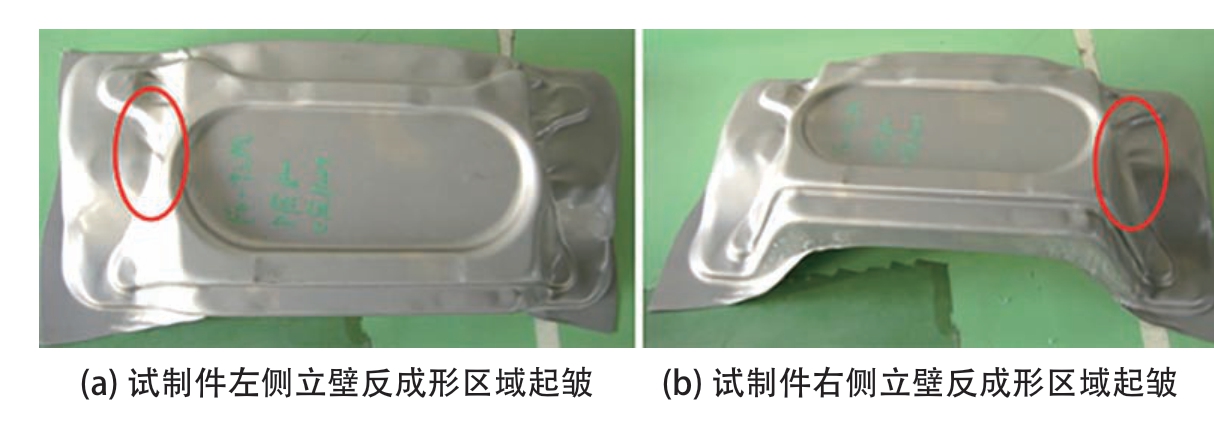
图4 试制中主体件成形状态示意图
⑷量产模具实际出件分析中,为了能够利用标准工装压出可以匹配装车的制件,用拉延模具进行压制,选用材料为比DP590R 成形性更好的TRIP600,并采取封闭成形,来控制试制零件回弹,零件初期出件,中间特征圆角区域开裂,增加阶段补料的工艺切口后,开裂消除,如图5 所示,标准工装在慢速油压机上一次性成形制件,定型比较稳定,但是两侧中部自由状态反成形区域出现起皱。
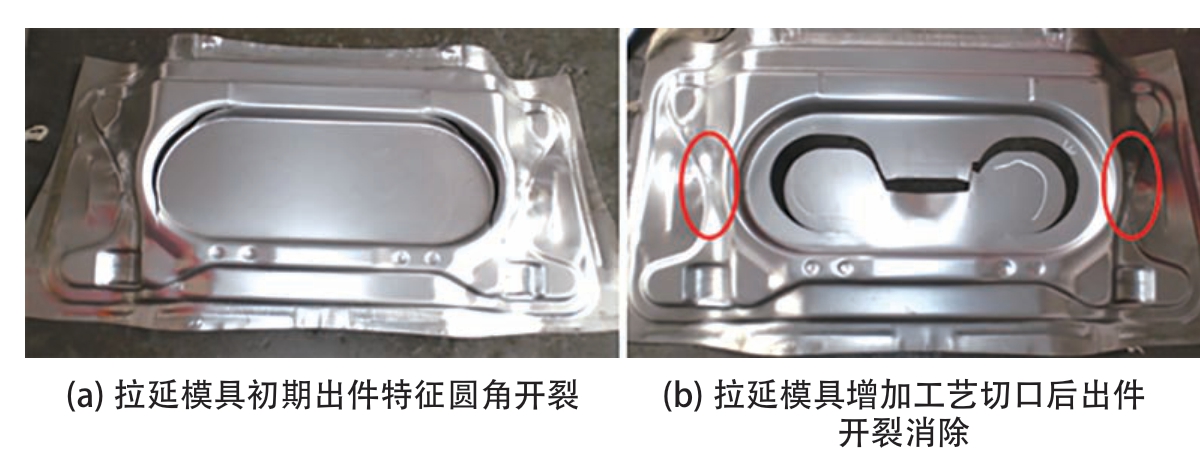
图5 实际主体件成形状态示意图
由于前副车架上部主体件本身就属于复杂成形件,再使用高强度板进行冲压,工艺排布上必须要合理,并且要有可以进行补偿的整形工序。实际出件后进行扫描分析,通过数据可以看出,由于造型复杂,成形深度相差较大,四角的回弹状态并不均匀,并且无论是试制件还是实际出件左右两侧中部自由状态反成形区域都存在起皱现象,位置一致对应。既然产品造型存在不对称,四角造型深度不一致,就要充分考虑成形不均匀导致的局部成形不充分。既要保证左右两侧中部表面成形充分无褶皱,又要保证四角成形回弹稳定,产品造型必须进行优化,在保证工艺通过性的前提下进行合理的造型修改;在定型稳定的前提下,对拉延模具进行合理的回弹修改。并根据工艺排布中各个工序的影响进行合理的研磨符型,保证全序出件不发生强行变形的假象回弹现象。
对策实施及确认
整体方案
前副车架上部主体件回弹扭曲调试时,考虑产品造型影响,确定拉延模具回弹修改方向,消除翻边整形模具回弹影响因素,在保证各个工序不发生强行变形的前提下,进行必要的工艺和模具修改,具体见表1。
一阶段方案实施并确认
⑴拉延回弹补偿设计。扫描数据显示的偏差,依据TRIP600高强板的回弹系数(550MPa≤抗拉强度≤650MPa 的高强板回弹补偿值取“回弹值的1.3 ~ 1.5 倍),计算得出回弹修改量,生成新的加工数据。
⑵ 拉延模具更改并出件确认。将拉延模具凸模立壁型面补焊,按照新数模加工,上模凹模镶块退火后,加垫片按新数模加工,压边圈保持原状态不更改,如图6所示,验证出件四角S面间隙量控制在0.75mm以内,但是四角回弹量不均匀。
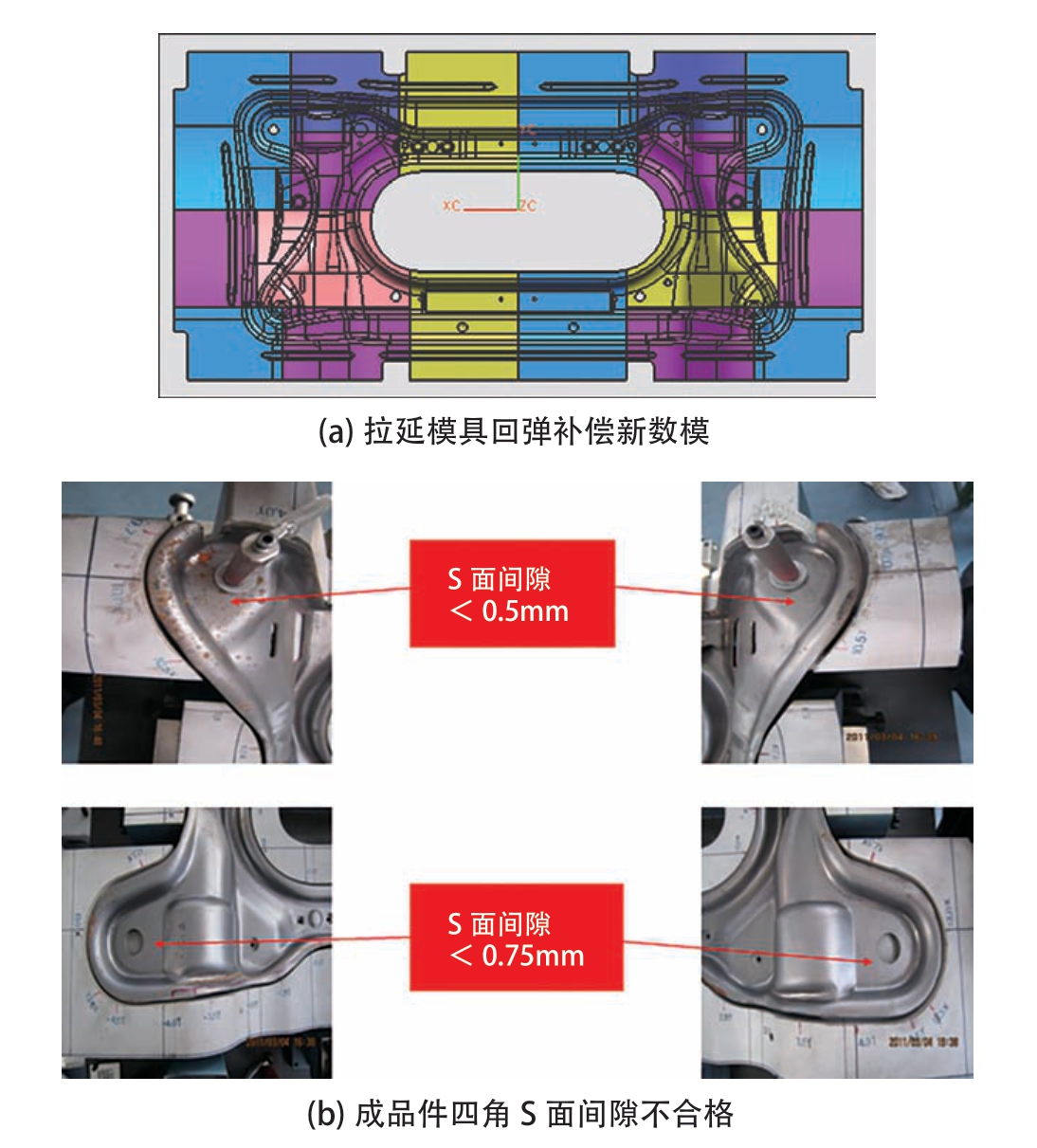
图6 拉延模具回弹补偿修改并出件确认示意图
拉延模具根据新的加工数据进行数控加工,拉延模具调整后要出件确认,四角S 面间隙量稳定在0.75mm 以内,未达到数据要求,前侧左右两角与后侧左右两角回弹量不一致,需要将四角S 面间隙量偏差做到非夹紧状态下0.20mm 以内。
表1 回弹扭曲调试方案汇总

二阶段方案实施并确认
⑴产品造型更改消除立壁褶皱。针对两侧中部自由状态反成形区域的起皱现象,在保证左右两侧中部表面成形充分,四角成形回弹稳定的前提下,对产品造型进行优化,增加三条吸塑筋,提高回弹稳定性,如图7 所示,产品造型增加三处吸塑造型。
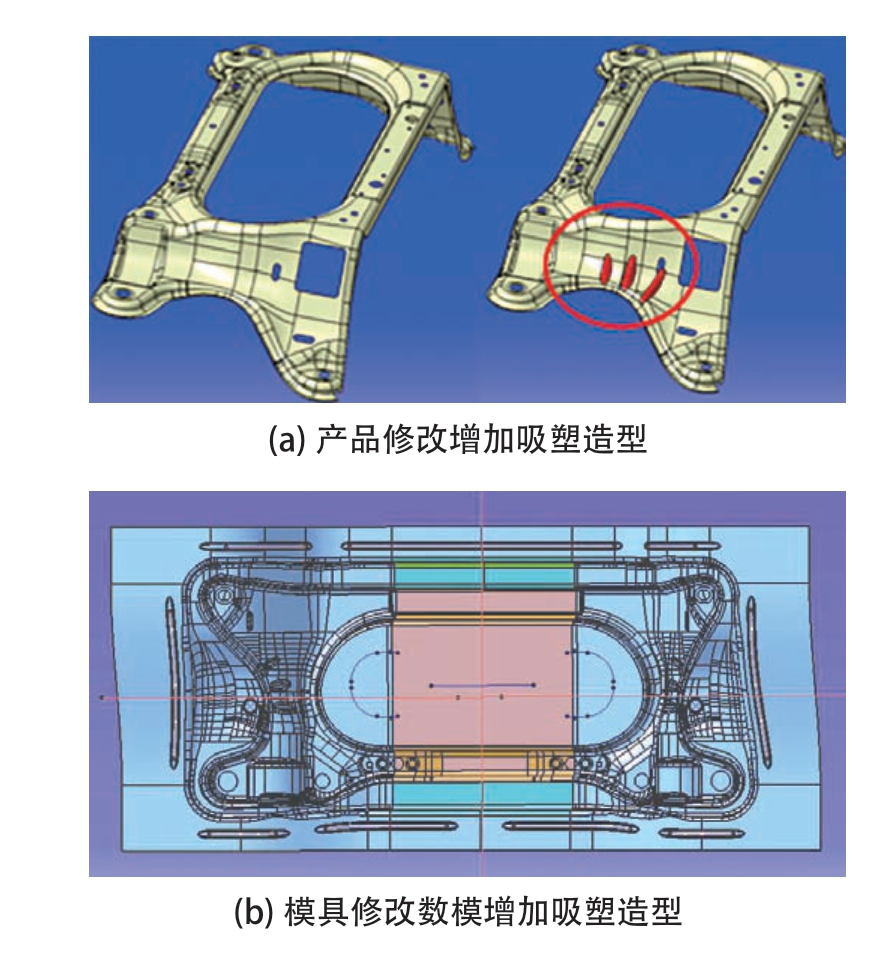
图7 主体件产品增加吸塑造型设计示意图
⑵拉延模具更改并出件确认。拉延模具凸模立壁型面补焊,按照新数模加工,上模凹模直接按照新数模加工,如图8 所示,验证出件四角S 面间隙量合理在0.20mm 以内,但是四角定位孔中心出现0.75mm偏移量。
完成修改后,拉延模具造成的四角S 面回弹已经稳定的控制在0.20mm,成品件出现孔位偏移0.75mm,左右两侧状态对应一致,这个时候可以考虑整形模具的因素,并进行相应的模具型面修整。
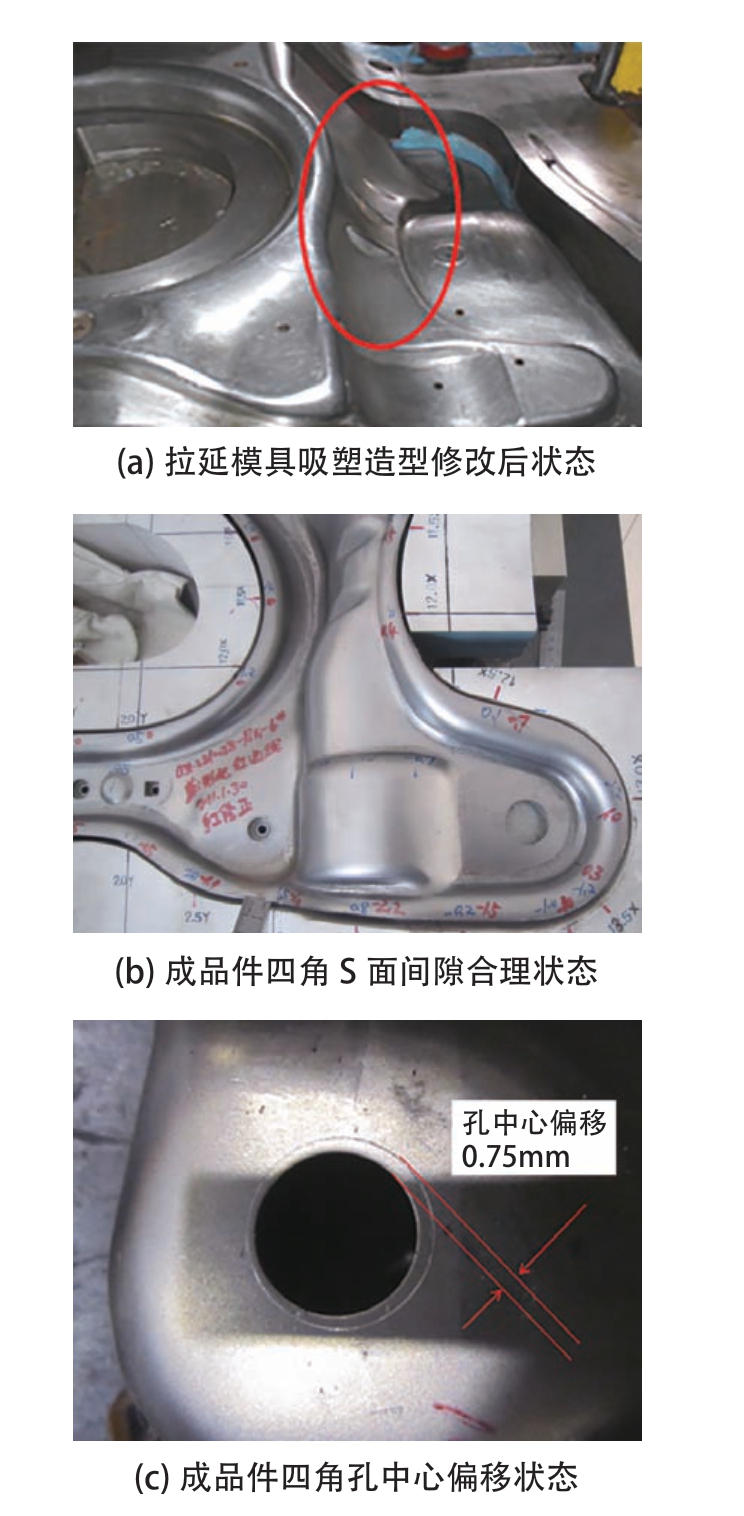
图8 主体件拉延模具新增型面修改并出件确认示意图
三阶段方案实施并确认
拉延模具回弹修改后拉延件回弹已经非常接近理论状态,但是批次出件仍有部分负回弹,所以对整形模具的上模型面圆角进行适当的修整,来消除整形模具型面对制件四角回弹的干涉点,如图9 所示。
调试至此,整形模具造成的回弹量变化已经消除,非夹紧状态下四角S 面间隙量已经稳定的控制在0.20mm 以内,孔中心偏移控制在0.3mm 以内,成品件批次回弹稳定,数据合格稳定,四角状态对应一致。接下来可以进行翻边不平且正回弹的修改。
四阶段方案实施并确认
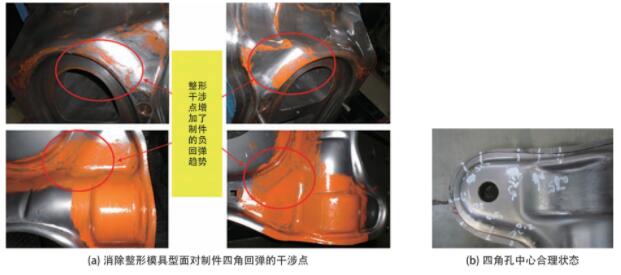
图9 主体件整形模具型面圆角修整并出件确认示意图
⑴翻边模具回弹补偿设计。前副车架上部主体件翻边翘曲回弹,激光焊搭接间隙为0.20mm,超差0.30mm,在保证四角数据不变的前提下,对翻边模具进行反向造型的回弹补偿设计,针对拉延成形完成一半深度,翻边成形完成一半深度的设计,回弹对应的翻边模具凸模立壁增加一条造型筋,反向造型补偿进行回弹校正。反向造型区域翻边间隙计算按照0.228 的数据进行反向造型的补偿设计,模具本体补焊数控修改区域按照0.20mm 进行造型高度设计,模具镶块加垫数控修改区域按照0.20mm+0.05mm(挤压缓冲量)=0.25mm 进行造型高度设计,造型宽度根据立壁弯曲区域宽度设计。
⑵翻边模具修改并出件确认。翻边模具凸模立壁两侧型面补焊,按照新数模加工,立壁中部型面镶块加垫后直接按照新数模加工,验证出件翻边立边翘曲回弹消除。至此制件整体出件状态稳定,经过产品造型修改、两侧拉延回弹修改、整形模具符形修整、翻边翘曲回弹修改,制件所有回弹区域状态稳定,四角回弹数据基本一致,达到冲压单件数据要求。修改过程即保持了批次出件稳定性,又保证了激光焊接质量,同时保证了整车安全性,如图10 所示。
结束语
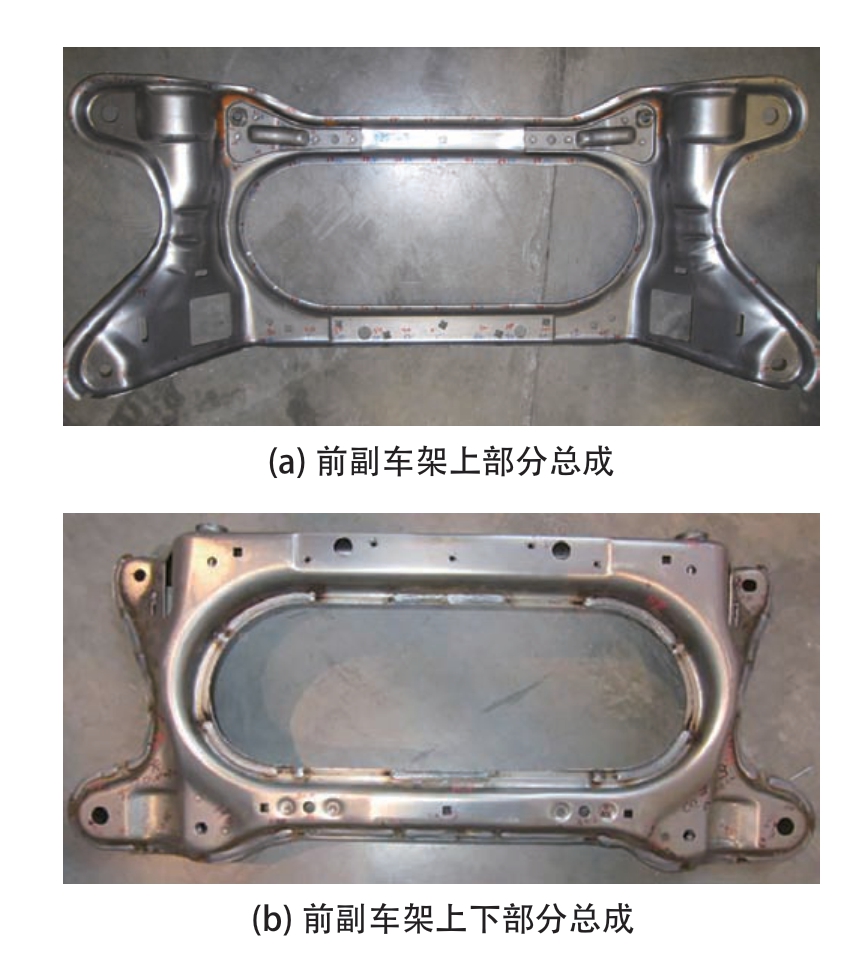
图10 主体件出件稳定且总成焊接质量合格示意图
通过复杂成形高强板回弹扭曲控制方法的研究,可归纳出高强板制件成形后回弹扭曲的调试思路:“合理的拉延回弹补偿、合理的整形符型消除强行变形、合理的翻边回弹补偿”。通过该思路可以很好的解决复杂成形高强板零件回弹扭曲问题,该思路简单易懂、清晰明了,可以有效的指导高强板零件调试。
赵锋
高级技师,从事冲压工艺与模具工作,主导完成车身外覆盖件表面质量优化的模具型面过A 面补偿方法的研究与应用,成为冲压核心技术,相关规范列入公司标准,公开专利5 项、专有技术5 项。
乘用车的安全性取决车架总成安全性,而整个车架总成中零件材料多为高强板,高强板零件尺寸的合格稳定直接决定车架振动试验的合格数据,下面将详细的说明通过零件扫描分析、提取回弹数据,并对拉延模具及整形模具型面进行回弹补偿修改,消除前副车架上部主体件回弹缺陷的方法。