侧围门洞内分模线对拉延成形的影响
文/王朋,姜长富,李艳·一汽-大众汽车有限公司成都分公司
冲压模具作为冷冲压生产的重要载体,其在生产中的稳定性,对制件的质量、生产成本以及生产效率有着重要的影响。随着轿车市场竞争的日益激烈,各个汽车生产厂家都把提高生产效率、降低生产成本作为一项主要的工作任务,本文主要介绍一汽-大众某车型侧围外板模具拉延稳定性的优化过程。
在批量的生产过程中,模具连续的拉深成形,导致板料在流动过程中与模具压料面之间摩擦生热,由于热胀冷缩造成凸凹模之间的间隙减小,增大板料的流动阻力,从而导致板料的流动速度发生变化。由于该模具门洞位置的分模线位置设置不合理,导致在拉延成形过程中板料敏感位置处于失控状态,加剧了模具的不稳定性,造成制件B 柱立面和法兰边交替出现缩颈、开裂的问题。通过此次对分模线位置的更改,使板料在成形过程中一直处于受控状态,确保模具拉延成形的稳定性,解决了零件B 立面和法兰边位置出现缩颈、开裂的问题。希望通过此案例可以给大家在调试过程中提供参考和借鉴。
问题描述
一汽-大众某车型侧围外板制件B 柱立面和法兰边交替出现缩颈、开裂问题,平均月停台时间178分钟,平均月废返品造成损失49852 元,再加上生产过程中压机的动能浪费、模修人员调试和生产人员备模的工时浪费等等。此问题已经严重制约了车间的生产效率和降成本的要求。图1 为制件B 柱立面开裂,图2 为制件B 柱法兰边开裂。
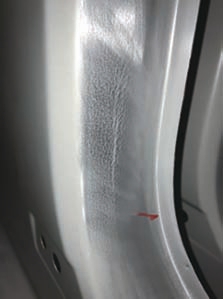
图1 侧围B 柱立面开裂
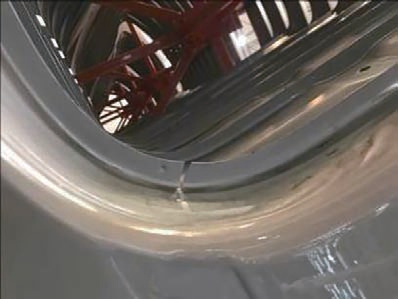
图2 侧围B 柱法兰边开裂
当零件立面出现开裂时,说明成形过程中板料流入量不够,需要增加板料的流入量。对应的方法为平衡块垫高、增加润滑或者减小下气垫的压力;当零件法兰边开裂时,说明成形过程中板料A、B 两处流入过快,且走料速度不一致(A 处>B 处或者A 处<B处)。对应的调试方法为平衡块降低或者增大下气垫的压力,保证A—B 之间压料面的压料力足够。所以,零件此位置立面开裂和法兰边开裂是两个矛盾体,在调整零件立面开裂时,平衡块垫高会导致A、B 位置板料流入速度加快,造成法兰边开裂;同时调整法兰边开裂时将平衡块降低,又会导致零件立面出现开裂问题。模具的稳定性不受控,很难找到平衡点,如图3 所示。
原因分析
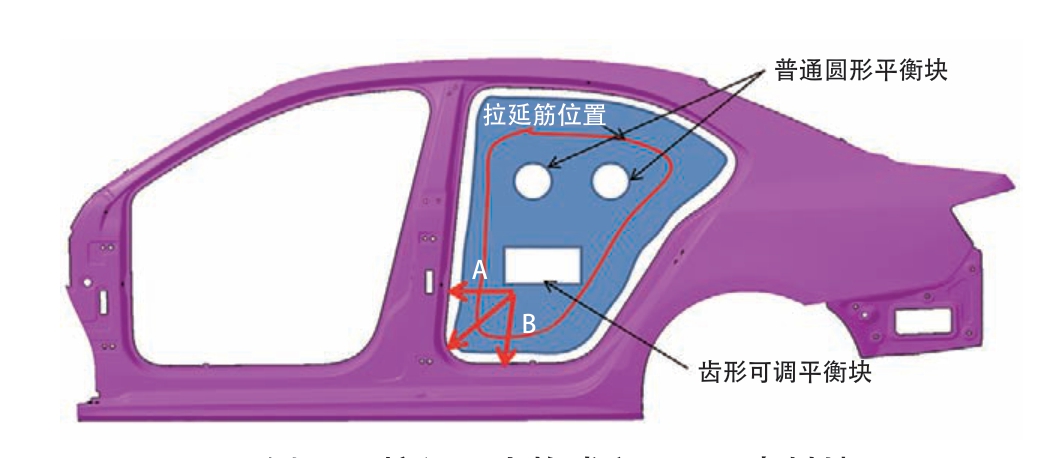
图3 侧围B 柱门洞内构成和A、B 走料情况
产品造型R 角太小,影响该位置板料的流动,此位置与后续工艺有一定的匹配要求,所以无法对产品造型进行更改;板料的机械性能参数状态不稳定,更换板料时导致频繁调试(每拍板料500 张,每批次生产需要更换5 次板料),所使用蒂森板料为德国进口板料,机械性能优化难度较大,短期内也无法实现;凸模与门洞内压边圈分模线设置不合理,导致标识位置板料在成形过程中一直处于失控状态(拉深高度为190mm,成形初期,门洞内压边圈在下气垫的作用下顶起190mm,而成形的关键位置却在整个拉伸过程中处于失控状态),属于模具工艺问题,可以通过数据模拟,根据模拟效果确认模具分模线需更改的合理位置(图4)。
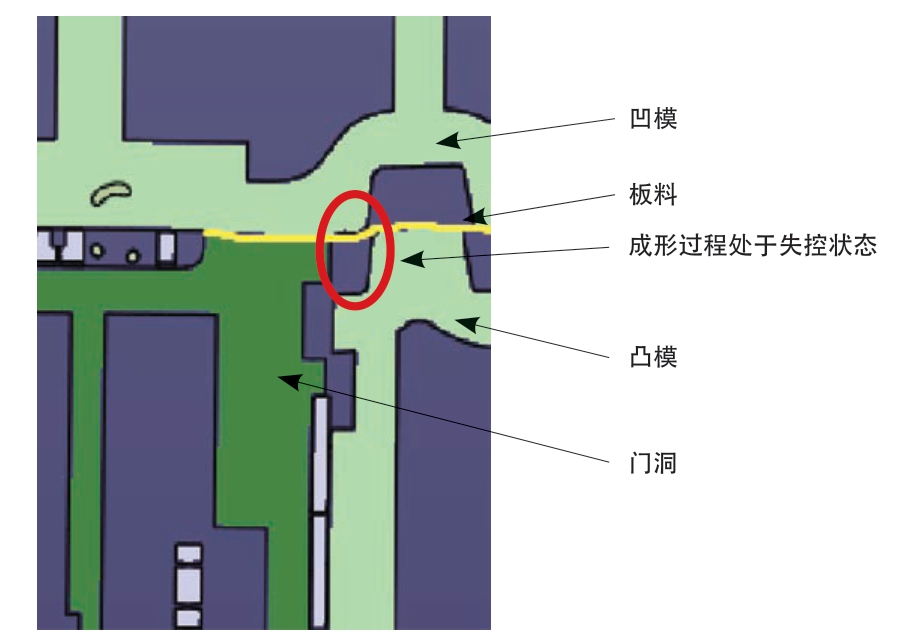
图4 侧围B 柱门洞内拉延模拟图
整改措施
根据拉延模拟情况,更改门洞内分模线位置,将凸模位置的分型面成形部位分给压边圈进行成形,使板料在成形过程中时刻处于受控状态,如图5 所示。
整改过程
⑴根据模拟情况,确认凸模分模线的位置,对凸模轮廓位置数控加工空开,如图6 所示。
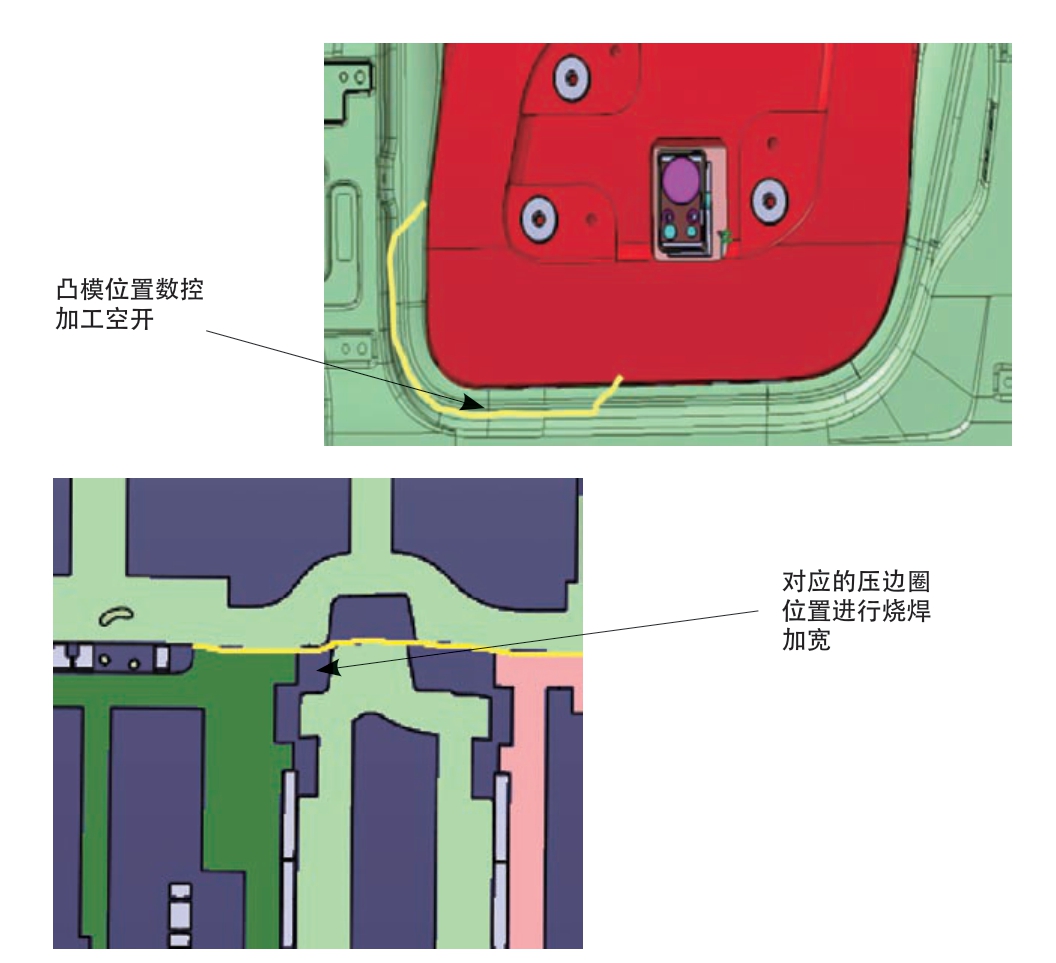
图5 侧围B 柱门洞内分模线更改图
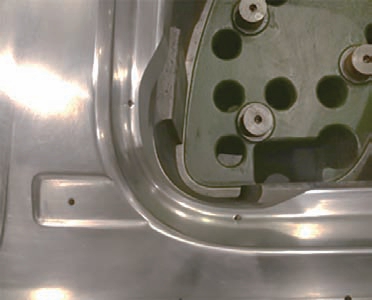
图6 凸模加工空开
⑵考虑到压料面整体从下至上进行烧焊加宽,焊接量过大,花费时间较长,且焊接变形太大,因此对该处压料面位置制作镶键,仅对表面进行烧焊,从而缩短整改时间,减少焊接变形。镶键嵌入模具基体内,并在下端增加支撑,可承受成形力,使用6×M16 的螺钉进行紧固,确保支撑的强度,如图7 所示。
⑶对压料面镶键位置进行烧焊。为保证镶键表面与原压料面无接缝,对原压料面整体降铣5mm,整体进行堆焊。焊条选用86FN 铸铁焊条,焊接前进行100 ~200℃预热,焊接时采用短焊道30 ~50mm,并进行充分锤击,消除焊接残余应力。焊接过程中,注意控制好焊接位置的温度,确保一次性完成焊接工作,中途不能长时间停息,防止冷却后再次焊接造成剥离现象。
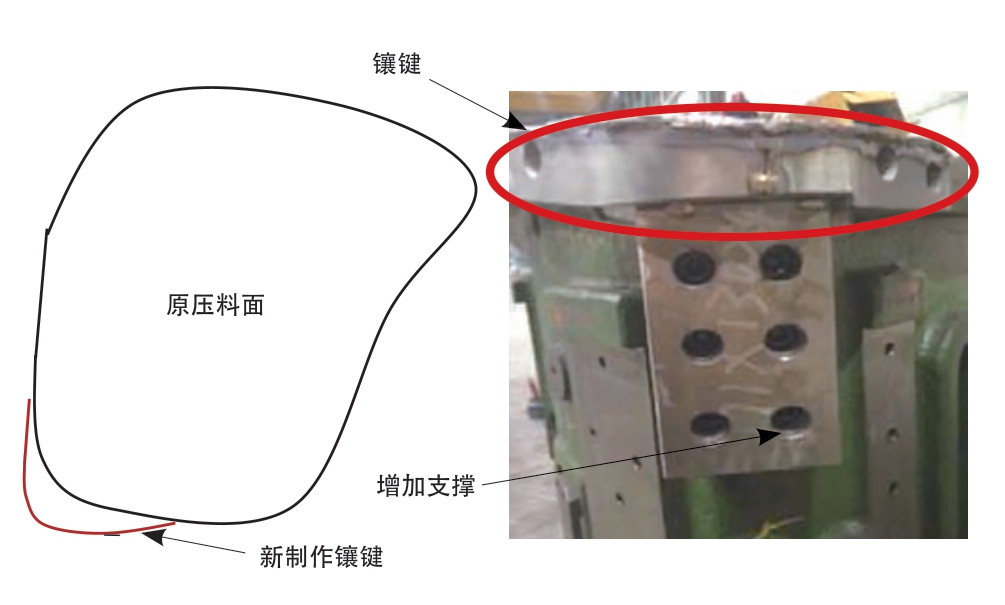
图7 压料面制作镶键
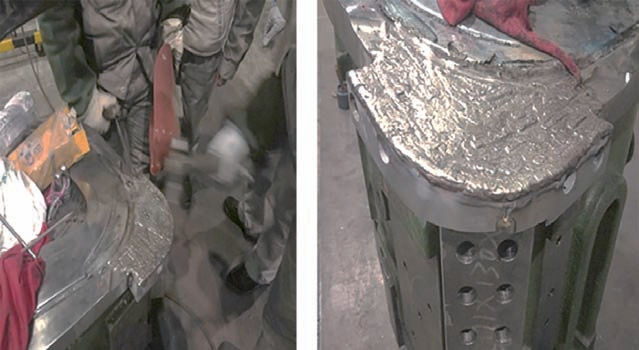
图8 压料面镶键位置焊接
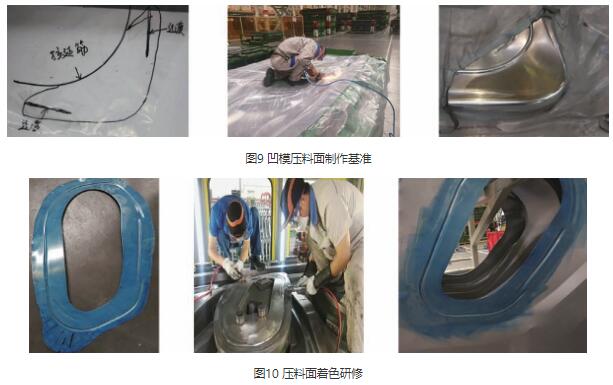
⑷凹模压料面对应位置进行研修,去掉台阶,研修光顺后作为基准,如图9 所示。
⑸检查测量凹模压料面与下模压边圈之间的间隙,根据着色情况,以凹模压料面为基准对下模压边圈烧焊位置进行研修,确保该位置着色均匀,如图10 所示。
整改后效果
通过此次整改调试,模具的稳定性明显提高,因此问题造成的停台时间和废返品基本消除,停台时间减少了84%,由于缩颈开裂造成的废返品损失下降了92%,达到预期的效果。
结束语
通过此次对大众速腾车型侧围外板模具分模线的更改,验证了拉延模在成形过程中分模线的位置对制件成形的影响,对后续在模具工艺设计时分模线位置的设置具有一定的参考价值,同时也给以后解决同类问题提供了新的思路和方向。
冲压模具作为冷冲压生产的重要载体,其在生产中的稳定性,对制件的质量、生产成本以及生产效率有着重要的影响。随着轿车市场竞争的日益激烈,各个汽车生产厂家都把提高生产效率、降低生产成本作为一项主要的工作任务,本文主要介绍一汽-大众某车型侧围外板模具拉延稳定性的优化过程。