行李厢外板上段偶发开裂原因及应对措施
文/赵维,黄义关,夏灿添,王永利·广汽乘用车有限公司
针对行李厢外板上段量产不稳定,偶发开裂问题,通过分析开裂原因,及Autoform 的相关参数调整模拟,制定了调整拉延筋、稳定压边圈间隙的措施。通过以上措施,使稳定生产的批量数由100 件出现开裂,提升至400 件不开裂。该方案可以为解决量产偶发开裂提供参考意义。
行李厢外板上段,是三厢车的行李厢外板组件之一(图1)。由于其造型原因,为避免滑移线等,冲压方向设置如图2 所示,导致牌照侧的拉延深度大(170mm)。深拉延在拉深过程中容易因各区域受力不均匀,导致材料流动异常,从而产生开裂缺陷。某车型实际生产100 至200 件,出现了偶发开裂(图3),需要不断通过实例积累经验和反复验证,才能找到有效的方法。
本文针对某车型行李厢外板上段量产偶发开裂问题,提出拉延筋参数管控及压边圈间隙调整方案,解决量产偶发开裂问题,同时建议在前期导入Autoform稳健分析,预防量产开裂问题,为其他行李厢外板开裂问题的解决提供借鉴和经验。
行李厢外板上段开裂的原因
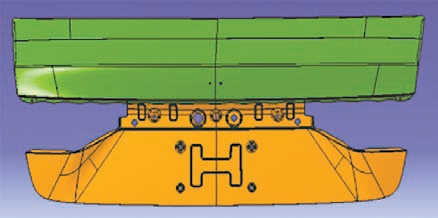
图1 行李厢外板
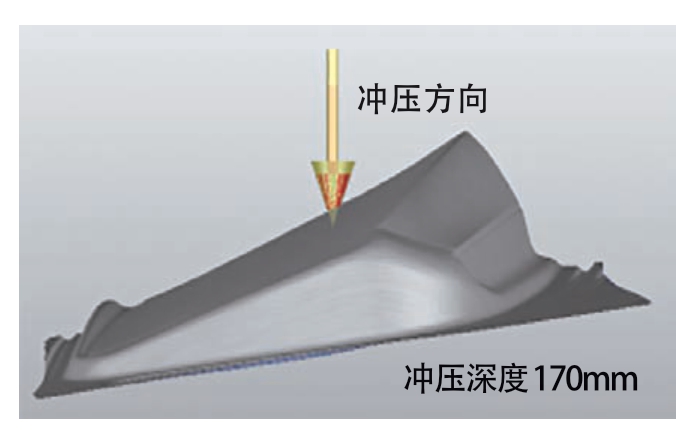
图2 行李厢冲压方向
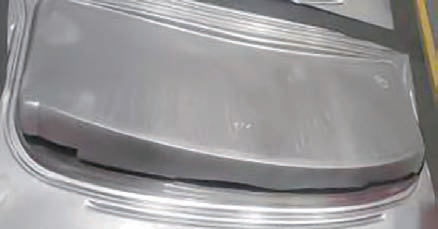
图3 行李厢外板开裂
表1 调整拔模角、入模R 角相应的参数

从影响拉延件成形开裂的各方面原因入手,结合该制件的特点分析开裂产生的原因及提出解决问题的途径。
成形开裂的常见原因分析
影响成形开裂的原因很多,根据实际现场可能出现的原因,主要归纳为以下6 个方面的原因:拉延深度大,导致流料不足,制件减薄超过成形极限;工艺补充,拔模角、入模R 角等过小,导致材料流动不足;拉延筋阻力过大,导致材料流动不足;顶杆压力不稳定,波动过大;模具研合率未达标,模具间隙不均导致材料流动异常;材料成形性能。
结合某车型行李厢外板上段进一步原因分析
其中拉延深度、顶杆压力对比其他车型零件,同样深拉延的侧围未出现开裂不稳定情况,因此从其他方面寻找原因。工艺补充方面,为了提高模具调试的工作效率,减少模具焊接、打磨等实际工作所带来的成本及风险。用Autoform CAE模拟分析,调整拔模角、入模R 角相应的参数(图4 及表1)。其中评价开裂稳定性的指标为MAX Failure(最大失效)。最大失效可以比较直观的衡量安全裕度,常规的最大失效指标标准为0.8,当小于0.8 时,认为安全裕度为20%,生产较稳定。当大于0.8 时,安全裕度小于20%,生产稳定性会较差。
按照表1 调整R 角及拔模角后,CAE 分析结果显示,开裂处的最大失效未在标准范围内,还是存在较大的开裂风险。判断整改R 角及拔模角无法解决不稳定开裂的原因。研合率决定了模具间隙,间隙对材料的流入有很大影响。
如图5 所示研合率整体达到90%;水平对比其他深拉延零件,已满足要求。虽然整体研合率已经达标,但还是存在局部硬点,这与模具本身的刚度、深拉延件材料流动过程相关,容易出现局部增厚,导致材料流动异常。后续为了增加稳定性需要考虑保证压边圈间隙能够大于1.1 倍料厚的措施。
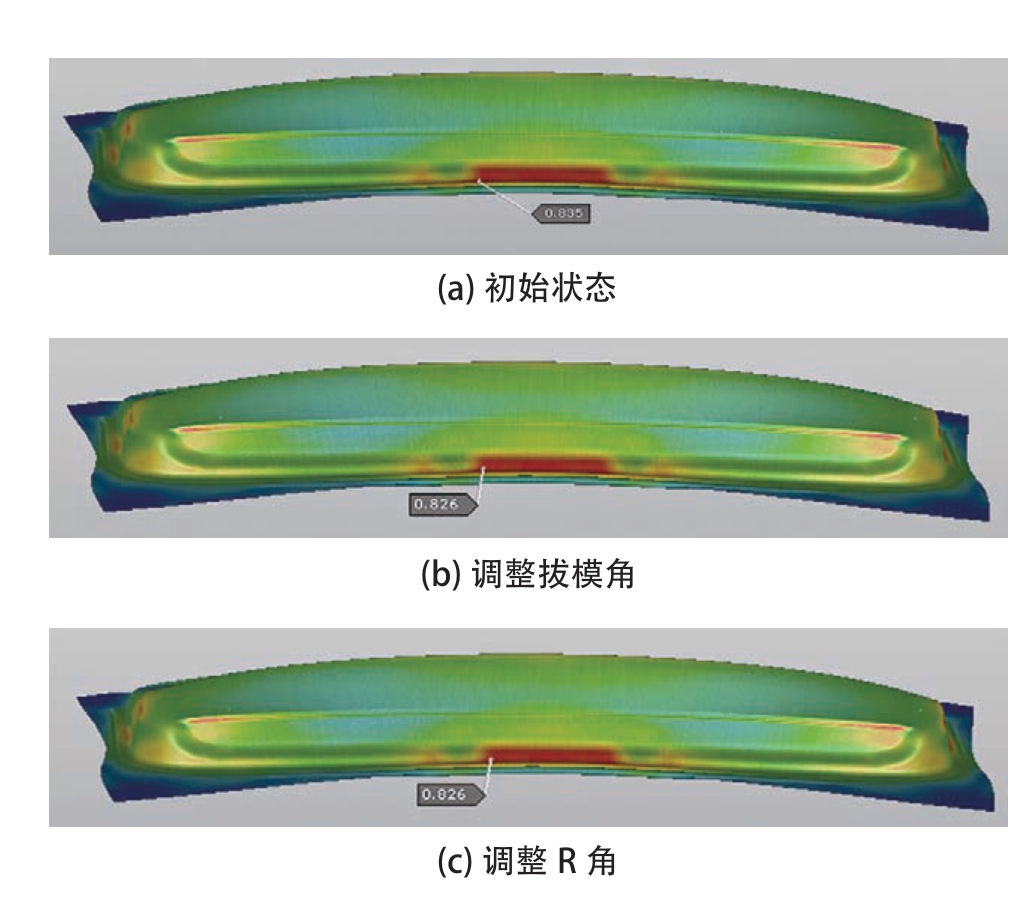
图4 初始状态、调整拔模角、入模R 角

图5 压边圈着色图
拉延筋、管理面状态(图6),拉延筋及管理面是控制材料流入的主要手段。拉延筋过紧或过松都会导致材料的流入出现异常,从而出现成形的不稳定。
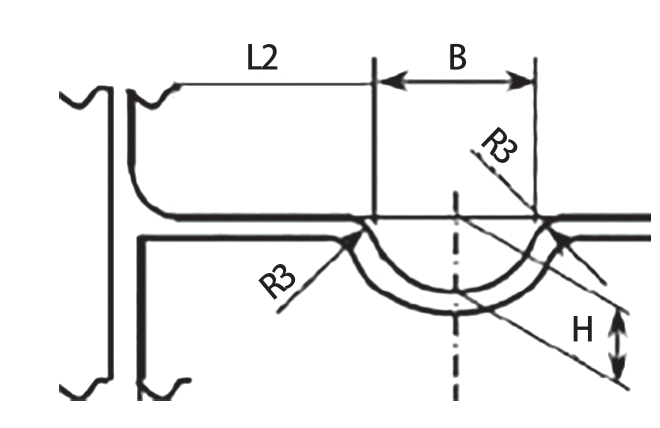
图6 拉延筋、管理面状态
材料成形性能影响成形性主要是屈服强度、抗拉强度、R、n 值等。通过行李厢外板其他车型横向材料性能对比(表3)发现,出现不稳定开裂的车型的材料屈强比相比稳定生产的车型的材料屈强比要大;材料屈强比对材料的冲压性能影响是很大的,而且也是比较重要的。小的屈强比对所有冲压成形都是有利的。在拉深时,如果板料的屈服点σs 低,则变形区的切向压应力较小,材料的起皱趋势也小。这时,防止起皱的压边力和摩擦损失都相应降低,结果对提高极限变形程度是有利的。通过Autoform 软件模拟更换屈强比较小的材料,结果显示零件的开裂程度指标由0.81 降到0.75,进一步证明了,使用屈强比低的材料,对生产稳定性有很大提高。
对策实施及效果验证
结合以上分析,得出压边圈间隙稳定、拉延筋和材料性能是导致开裂的主要原因。材料性能决定了工艺的裕度范围,压边圈间隙、拉延筋等工艺参数保证生产在安全裕度范围内波动。由于条件限制,材料更换暂不考虑,主要针对拉延筋、压边圈间隙稳定进行相关对策,保证生产零件能够在现有的安全裕度范围内波动,提高生产的稳定性。
⑴调整拉延筋,修复至合格范围内,调整后间隙为0.8mm,筋高为6mm,如图7 所示。
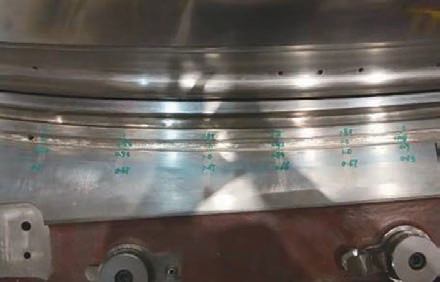
图7 调整后间隙
⑵调整平衡块,保证压边圈间隙大于1.1 倍料厚,从而保证生产的稳定,不出现开裂情况。通过垫片可以实现平衡块的调整。
⑶监控F 侧与出料侧材料流入量差异状态。生产首件、100 件、200 件、300 件各阶段监测流入量,得出以下流入量的合格区间(图8)。通过爬坡式的生产(100 件、200 件、300 件),发现流入量异常点,针对异常点,对压边圈进行相应的去硬点研合。当出现流入量不在此区间,需要调查模具状态。针对差异点进行模具分析。
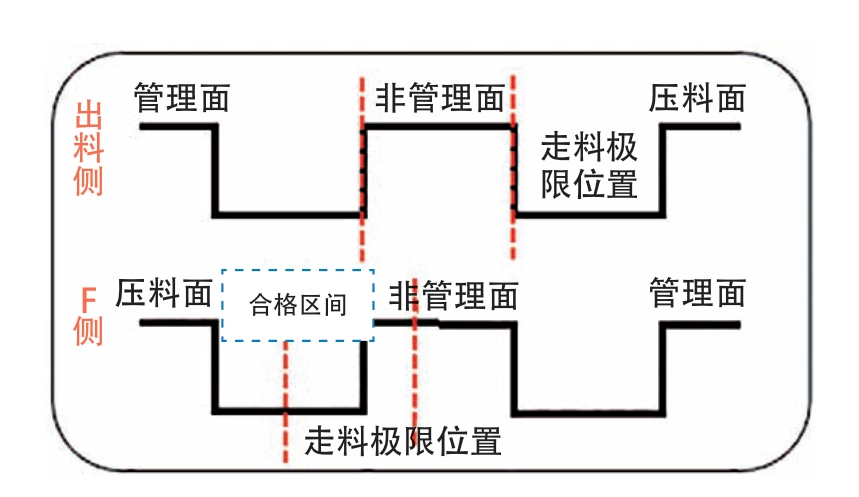
图8 材料流入量指示图
经过一系列措施,使零件生产400 件未出现开裂情况,满足了生产的批量需求。材料性能方面决定安全裕度范围,材料选择需要在同步工程前期考虑生产的稳定性问题。如何在同步工程阶段发现材料及工艺的不稳定性?通过在Autoform 中引进Sigma 模块是一个很好的办法。
同步工程建议
Autoform 运用Sigma 分析,设置不同的参数,压料力、摩擦系数、材料性能波动范围,检证工艺是否稳定(图9)。通过Sigma 分析,有效模拟现场的可变因素,可以检验工艺是否稳定(CP 值大于1.33),在同步工程阶段完成工艺改善、产品优化及材料的选择。
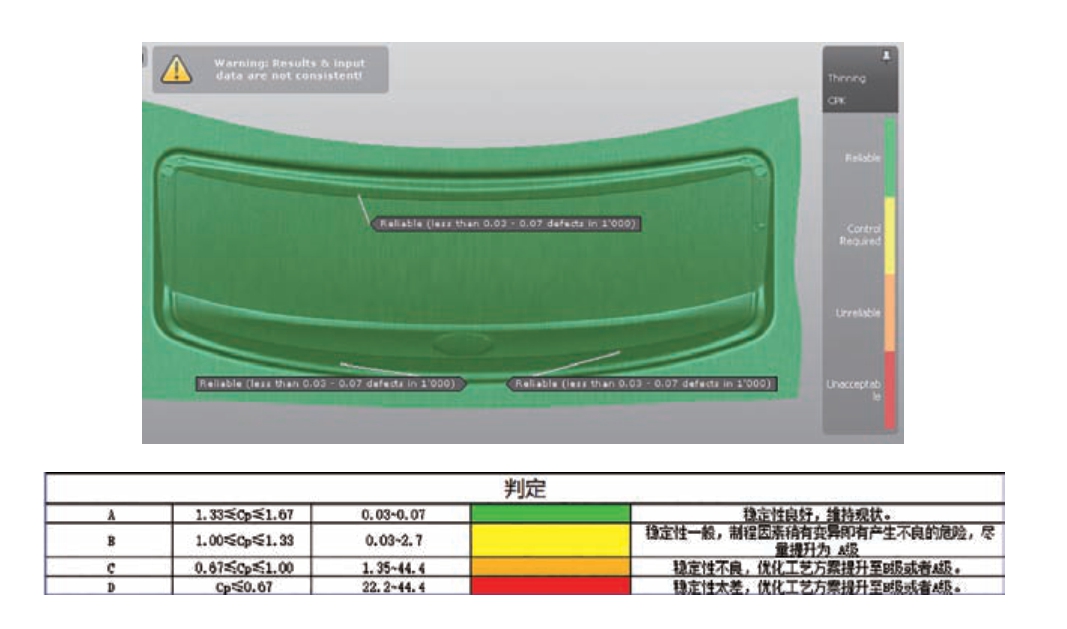
图9 稳定性结果评判
结束语
模具调试期间行李厢外板上段通过对开裂原因的分析,针对性的对拉延筋、压边圈间隙稳定性进行调整,实现了模具由100 件出现开裂提升至400 件不出现开裂的稳定生产。为了生产的稳定性,减少调试周期,前期同步工程就需要进行相关优化工作,需要引进Autoform 进行多参数波动模拟的Sigma 分析,能够有效模拟现场的可变因素,识别相关风险,早期进行工艺优化或者材料的选择。
针对行李厢外板上段量产不稳定,偶发开裂问题,通过分析开裂原因,及Autoform 的相关参数调整模拟,制定了调整拉延筋、稳定压边圈间隙的措施。通过以上措施,使稳定生产的批量数由100 件出现开裂,提升至400 件不开裂。该方案可以为解决量产偶发开裂提供参考意义。