论覆盖件拉延模拉延筋作用及其同材再造
文/田卓华·北汽福田汽车股份有限公司
马超,曹翔宇,黄晶晶·北汽福田奥铃汽车厂
自2013 年以来,国内汽车产量一直保持在2000 万辆以上,无论车身设计还是制造质量均已接近发达国家汽车制造水平。但是,一些复杂车身覆盖件拉延模设计与开发仍需进一步提高。车身覆盖件拉延模对于合格拉延工序件具有举足轻重的地位,常言道成也拉延,败也拉延。
覆盖件拉延破裂或皱纹是工艺补充和压料面联合作用的结果。常常受制于开发经验的不足及CAE 分析软件的局限性,复杂拉延工序件工艺设计有时不尽完美,困扰着汽车模具制造水平的提升,即使在现代计算机虚拟分析已经十分普及的今天。因为,再先进的分析软件,都是设计师的工具和助手,借助分析系统能够快速虚拟显示、证明设计师的匠心独具,助力造型设计极致完美。
主要有三个要素迫使拉延模工艺造型设计急待变革。首先,复杂覆盖件模具制造调试阶段,产品表现瘪塘或波纹,需要局部增添或加高拉延筋;其次,总有一些调试钳工急于求成,仓促打磨,毁掉拉延筋或其一部分,但是根本问题并没有完全解决,甚至出现新的缺陷,往往需要恢复拉延筋;再次,服役模具经过数十万次冲压,拉延筋磨损,也需要再造拉延筋。
上述增添、恢复、再造拉延筋三种模态,本质是压料面凸筋需要堆积材料,另一侧去除材料。堆积拉延筋,大多采用比较节约的焊接工艺。堆焊筋常常有焊接气孔和裂纹,二者都是破坏拉延表面及增阻的罪魁祸首。尽管有先进的工艺,诸如激光烧结、凝结粉材工艺,迫于多种原因始终没有普及。改变拉延筋方向,可以容易重构拉延筋。改变拉延筋方向设计,势在必行,功在设计之变革,利在当下与未来。
拉延筋传统再造
拉深力主要由拉延筋产生,拉延筋的阻力可达到拉深力的98.5%,如图1 所示。车身地板拉延工艺设计,CAE 分析压料力120t、拉深力1000t,摩擦系数0.15,拉延行程400mm,材质DC06-0.8。
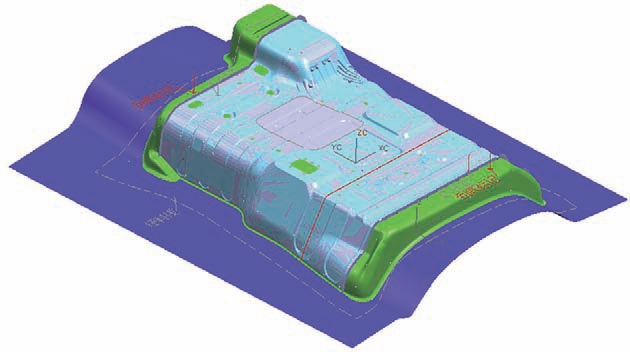
图1 车身地板拉延工艺设计
无论是新制作模具还是服役多年的模具,拉延筋难免需要重构。图2 为某车型发罩外板,拉深工序件侧部波纹,经过修边、翻边工序后的产品波纹趋势和拉延完全一致,如图3 所示,检测型面误差用红色数字表示,约500mm长的范围内,波纹在-2.8~1.3mm之间波动,面差最大波动4.1mm,发罩左右两侧波纹基本对称。

图2 拉延工序件

图3 发罩外板侧部波纹
借助于CAE 分析软件,在设计阶段,许多拉延造型能够虚拟显示破裂与吸颈、起皱与波纹,设计师会把拉延筋及工艺补充造型做到尽善尽美,在产品及模具合格的前提下,实体验证与虚拟分析基本一致。但是,现实中总有一些在虚拟世界难以精准把握的产品,一旦在模具验证阶段表现不良,经常需要增加一条拉延筋。再造凸筋,最简易的办法是堆焊。堆焊凸筋常见弊病是气孔和裂纹,且很难彻底杜绝,最致命的是堆焊材质与基体不同,由于热应变,模具表面强化处理往往出现二次裂纹。
造成拉延筋重构的原因有以下两点,导致新开发模具增添拉延筋的概率升高。
⑴CAE 分析软件本身有局限性,即虚拟拉延过程认为模具是刚体,即受力状态不变形。实际是覆盖件拉延模在力的作用下发生形变及位移。有人曾经用数控铣床检测卡车门板模具在重力作用下的变形。在数控铣床工作台面,模具基本夹持长度的一半,另一半悬空,检测出Z 向下垂0.07mm,一般模具结构尺寸越大,下垂越大。因为冲压件结构不同,模具结构也不同。即使产品结构类似,各模具厂设计标准不统一。所以,CAE 软件系统无法定义模具结构力学模型,受力变形无法计算。这是分析软件系统最大的局限性。
⑵复杂覆盖件建型及分析取决于设计经验。经验不足,有时难以发现风险所在。如图4 所示的发罩拉延工序件,调试阶段产品左右两侧波纹较大,局部流料过快是造成侧壁波纹的原因。模具出厂前,压料面堆焊增添一条筋,局部变为双筋,波纹范围内红色线条表示增添的筋。

图4 发罩拉延工序件
拉延筋便捷再造
打破传统设计理念,改变拉延筋方向,凸筋在下,凹槽在上,使重构拉延筋变得非常简洁又可靠。最重要的是拉延筋在基体上生成,与模具同材。图5 为改变方向的拉延筋结构。无论是新模具还是旧模具重构拉延筋十分便捷,从源头规避了堆焊缺陷。
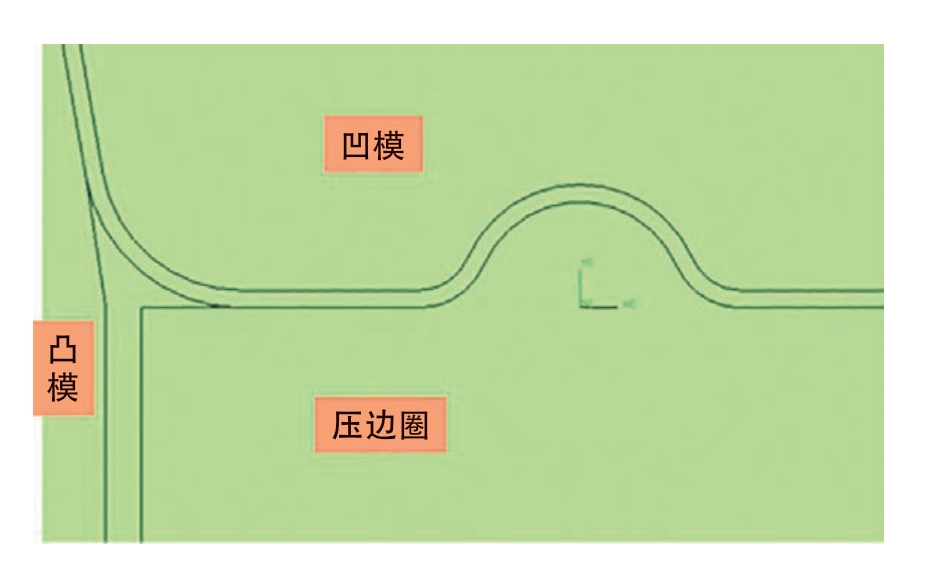
图5 改变方向的拉延筋结构
凸筋在下,即在压边圈上,凹槽在上,拉延筋增阻效应并未改变。模具调试阶段若需要增加筋,只要数铣降型,凸筋浮出,无需补焊,同时压料面调整垫安装面同等降低;凹槽在凹模压料面铣出。如此改造,模具闭合高度依然不变。如果在服役模具需要同材恢复筋,只需要数铣压料面,上模无需做任何改动。对于严重磨损的模具,若考虑凹槽口两条棱线的磨损,也无需补焊,只要凸筋适当增高,比模具初始设计筋高,或改变圆筋为梯形筋,能够抵消凹槽磨损的不利因素。当然,凹槽也要做相应变更,仅仅是凹槽。
传统设计理念,凸筋在上,若模具使用方不接受补焊,压料面及整个凹模型面都要降型,数铣量是压边圈压料面的几倍到数十倍,且模具闭高发生变化。
超级模具调试,在CAE 分析基础上,筋的重构再造及其他任何型面变更,全部依靠数铣完成。拉延模压料面和筋的微调,不再手工打磨。打磨不仅不精准、不一致,让交付后的模具维修没有数字模型,无法传承。
也许有人担心凸筋在下,影响板料定位。实际大可不必有此担忧,因为,板坯定位依靠四周定位板已经十分稳定,理论上定位板有效定位增加一个凸筋的高度,约4.0 ~6.0mm。只是板料接触压料面面积较小,筋的顶面撑起板坯与压料面有间隙,拉延增阻和筋在上模完全一样。无论凸筋在上或在下,压边圈升起,滑块下降接料,都是在底缸压力作用下板料先生成筋,滑块继续下降,板料流过筋产生阻力,即拉伸力。
深拉延模具和高强度板拉延模具,筋的磨损较快,每当冲压一定量,磨损致使拉延作用降低或失效,为便于恢复,凸筋在下,容易数铣降型再造。由于是本体材质,彻底规避焊接裂纹、气孔等缺陷,更不会有日后表面强化处理导致焊接部位出现二次裂纹。通常压边圈压料面厚度为50mm,降型恢复凸筋,极限情况最大减薄一个筋的高度。开发设计压料面和调整垫座面时,厚度预留5 ~8mm,即压料面厚度为55 ~58mm。
覆盖件拉延模几乎全部采用倒装结构,工作时凹模在上,凸模及压边圈在下。拉延筋的传统设计概念,起源于开发经验不足和数控铣床资源稀缺。在上模压料面设计凸筋,下模压边圈设置凹槽,之所以如此设计,是假设凸筋正确,只动下模凹槽,便于人工打磨。图6 为拉延模压料面传统筋布局。形成传统拉延筋的原因有以下三个。

图6 拉延模压边面传统筋的布局
⑴调试方便。20 世纪80、90 年代,拉延模凸筋在上,凹槽在下,认为便于钳工调试打磨。相反,凹槽在上,仰打不方便,沙灰侵染面积较大。这个习惯,貌似简约,其实不然。简单的前提是假设凸筋不改,需要加速进料,只好打磨、放大下模凹槽口部棱线R以降低阻力。若需要增阻,绝对不简单。增补凸筋,或增高凸筋,调试依然是先堆焊,再仰打。钳工劳动强度大,环境污染严重。从大概率事件来看,旧的设计模50%打磨下模凹槽,50%打磨上模堆焊凸筋。
⑵资源稀缺。那时,数控铣床刚刚起步,人工调试打磨十分普遍。能够手工改造的,绝不用数控铣床;但是,丝毫顾及不到手工变更型面是不可传承和复制的。
⑶标准较低。那个年代,CAE 分析基本处于初级阶段,精准度较低。筋的再造全部采用补焊工艺,堆焊气孔和裂纹较普遍,主机厂不得不让步接收。
结束语
本文论述拉延模拉延筋增阻原理。车身模具开发过程及在用拉延模功能恢复,拉延筋免不了重构,改变拉延筋方向使其再造更容易,拉延效应同材恢复更便捷。如果沿用过去的设计结构,拉延筋堆焊工艺出现大量气孔和裂缝,导致拉延拉毛、拉裂、摩擦力增大;也因为焊材与母材的差别,模具表面强化处理受限。
时代在发展,技术在进步,国内汽车模具飞速发展,质量水平不断提高,模具制造必须紧跟时代步伐,变革设计标准,才能满足主机厂日益增长的模具及覆盖件的质量要求。变革拉延筋设计方向简单易行,同材质的拉延筋重构必定深受主机厂青睐。
田卓华
北汽福田汽车股份有限公司副总工艺师,高级工程师,从事汽车覆盖件模具开发设计25 年,获得国家发明专利两项,实用新型专利2 项。
自2013 年以来,国内汽车产量一直保持在2000 万辆以上,无论车身设计还是制造质量均已接近发达国家汽车制造水平。但是,一些复杂车身覆盖件拉延模设计与开发仍需进一步提高。车身覆盖件拉延模对于合格拉延工序件具有举足轻重的地位,常言道成也拉延,败也拉延。